プロダクトストーリー
Fleepは、陸前高田市にある自社工場のシェリールで主に縫製されています。
とてもデリケートな素材、スマイルコットン®で作られているFleepは縫製にも高い技術を要します。
各担当者の声と共に、そのプロセスをご覧ください。
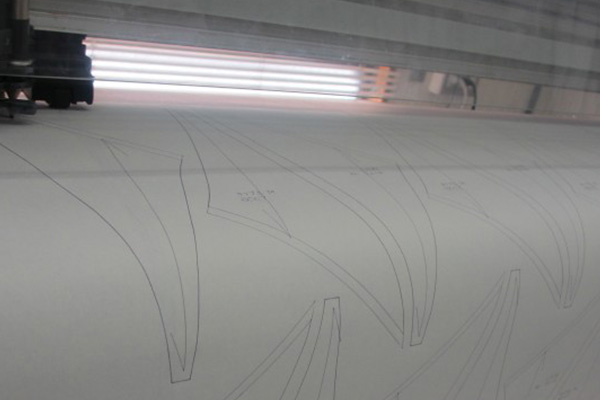
Fleepのデザインとパターンメーキングは、秩父市の本社で行われ、そこで完成したパターンが、縫製工場のPCに送られます。そのパターンのデータを生産数に応じてマーキング(パターンを生地巾に合わせてレイアウトすること)して、プロッターから出力します。
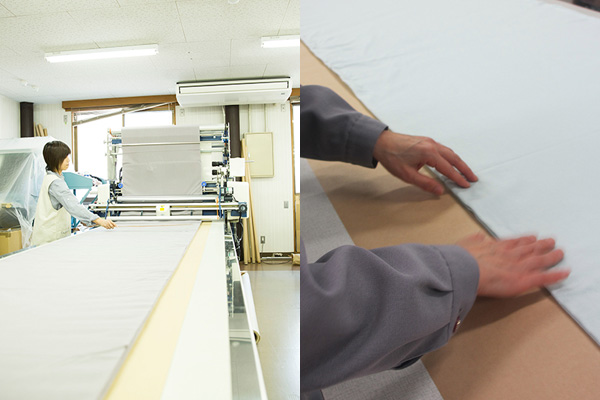
巻いたりたたんだりして納品された生地を、裁断しやすいように、生地巾に応じて2台の自動延反機を使って広げ、重ねていきます。「寸法通りの商品に裁断・縫製するために、生地の縮みや余計なクセを取り除くのが延反です。ハリのある素材なら、延反機が布を広げるのを待つだけでいいのですが、スマイルコットン®は軽くて柔らかいため、布が重なったりシワになりやすいんです。それを目で見てチェックし、手で伸ばしていきます。手が荒れていると繊維に引っかかり傷をつけてしまうため、日頃から注意しています。気になる場合は薄手の手袋をして作業することもあります」
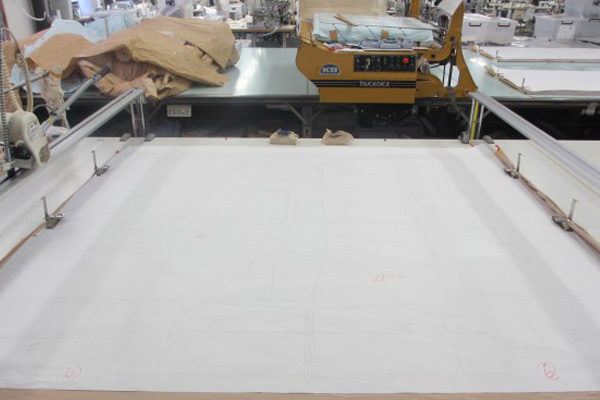
出力したパターンを、延反した生地の上に配置します。
「通常の生地だと25枚程度重ねますが、スマイルコットン®は多くても20枚程度。柔らかく滑りやすいため、どうしても重ねる枚数は少なくなります。そのぶん効率は悪くなるのですが、裁断でミスがあると後の作業すべてに影響するため、慎重に行います」
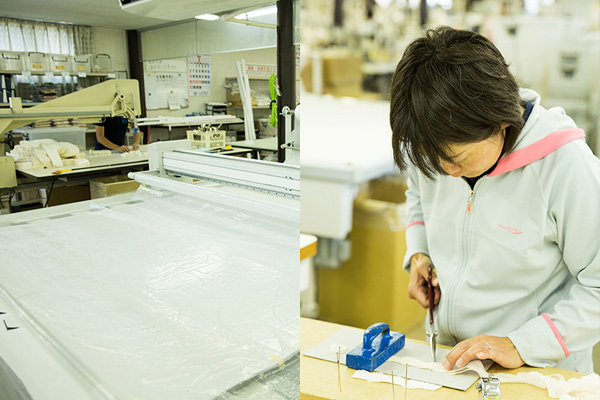
自動裁断機(CAM)を使用して細かいパーツ毎に、生地を裁断します。
レースは巾、柄の大きさや方向性によってパターン配置が変わるため、細かい手作業での裁断が必要になります。

主力となる陸前高田市の縫製工場では、7種類のミシンが約100台並んでおり、約60名が一針一針、着用していただく方々のことを想いながら、心を込めて縫製しています。Fleepの商品はシンプルに見えても、肌あたりを考慮した複雑な縫い方になっていて、多いものでは40工程以上になります。

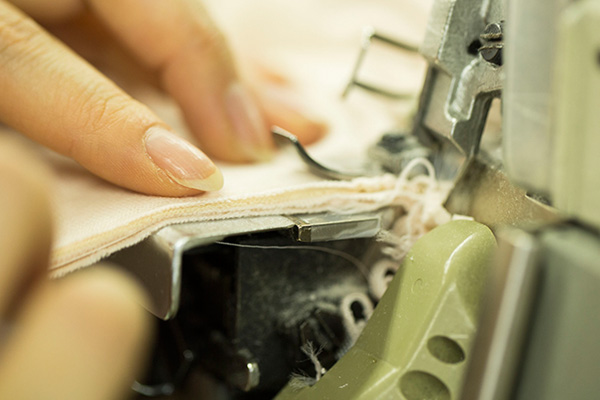
「Fleepが誕生した2007年から担当しています。それまでも下着を縫っていたので、伸縮性のある素材や薄い素材には慣れていましたが、スマイルコットン®の柔らかさに、最初はとても苦労しました。
縫うときの布を引っぱる加減などが、他の素材とはまったく違うんです。たぶん通常の2倍くらい時間がかかっていたと思います。始めは納期に間に合うか、本当に心配でした」
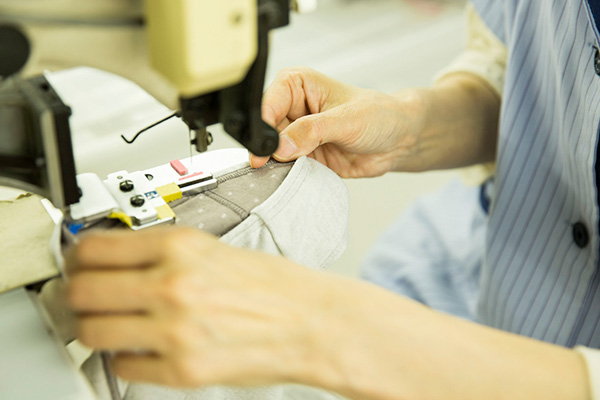
「1989年からこの工場で下着を縫っていますが、スマイルコットン®を初めて縫ったときは、その伸縮性の感覚をなかなか掴めませんでした。
今まで扱った中でいちばん苦労した素材、と言えると思います。縫いしろ部分をフラットにするためには、この柔らかくて滑りやすい素材を6枚重ねて縫うこともあります。
始めは苦労しましたが、満足できる仕上がりになってからは、他の素材を縫うより楽しくなって。不思議なものですね(笑)」

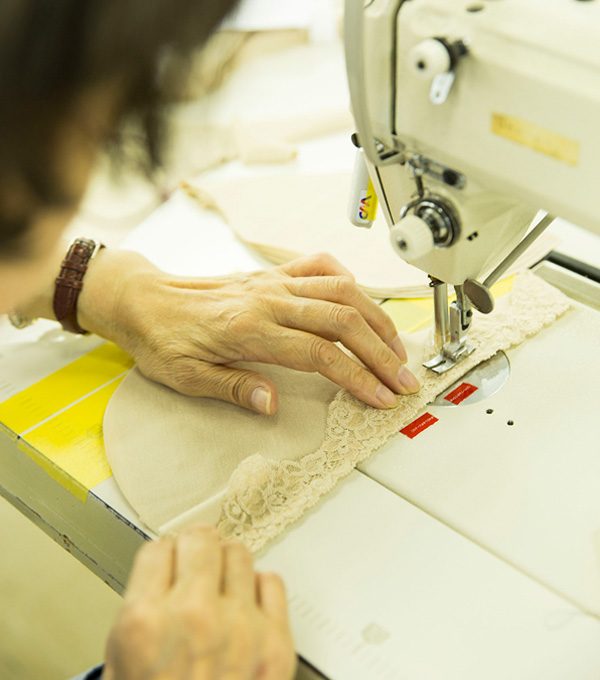
「Fleepの縫製は、他の製品に比べて工程が多いのが特徴です。工程が多いということは、ひとつの工程でわずかでもズレが起きると、それが少しずつ重なって最終的には大きなミスになるということです。
“最初のひと針がいちばん大切”。チーム全員が、その気持ちで縫っています」

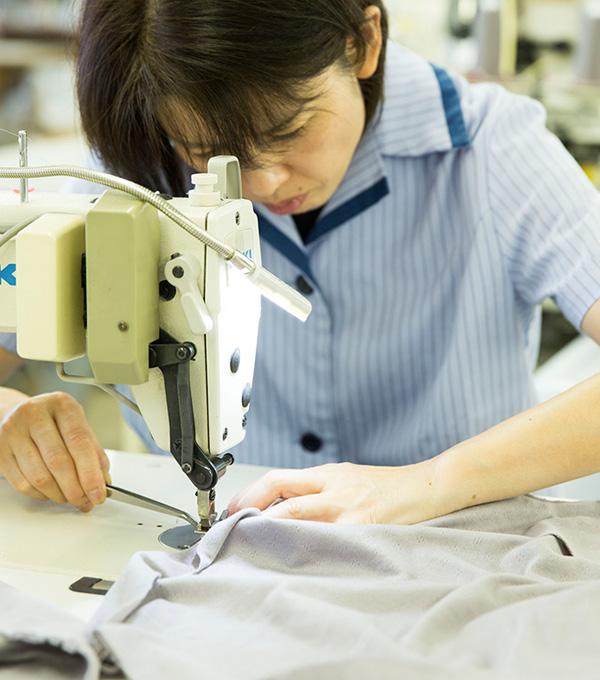
「Fleepは縫い目を表に出して縫製します。つまり、普通の製品とは表裏がすべて逆なんです。 縫製に慣れている者ほど、始めはこれに戸惑い、慣れるのに時間がかかりました。
途中で『表裏を間違えている!』と、ハッとしたことが何度も。今では、Fleepの縫製に関わる全員が、それを体で覚えています」
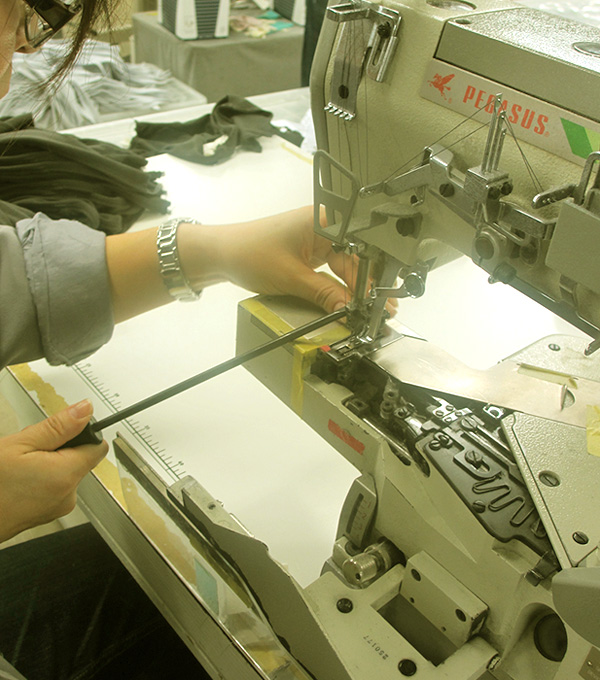
「重ねた生地の枚数、縫う箇所によって、ミシンの目調子を微妙に変えています。濃色は目調子を少し緩くしたり、同じ生地でも色によって加減が変わるんです。それは、生地と会話しながらの作業という感じですね。少しでも縫いやすいように、機械担当と相談しながらミシンのアタッチメントを改良することも。皆で工夫しながら、縫製の現場でも改善を重ねています」

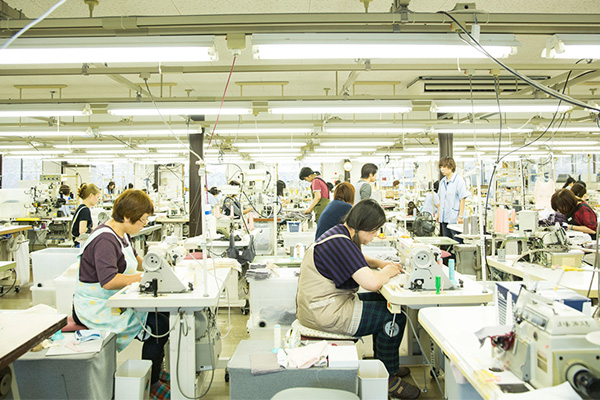
「通常、衣類の生産というのは、作業の内容と流れを固定して、一人が同じ場所で同じ工程を繰り返し行うほうが、効率が良く生産性も上がります。でも、Fleepは縫製の内容が細かいため、固定したラインをあえて設けず、フレキシブルに組み替えています。それが互いの仕事を理解することにもなって、チームワークも強くなるようです」
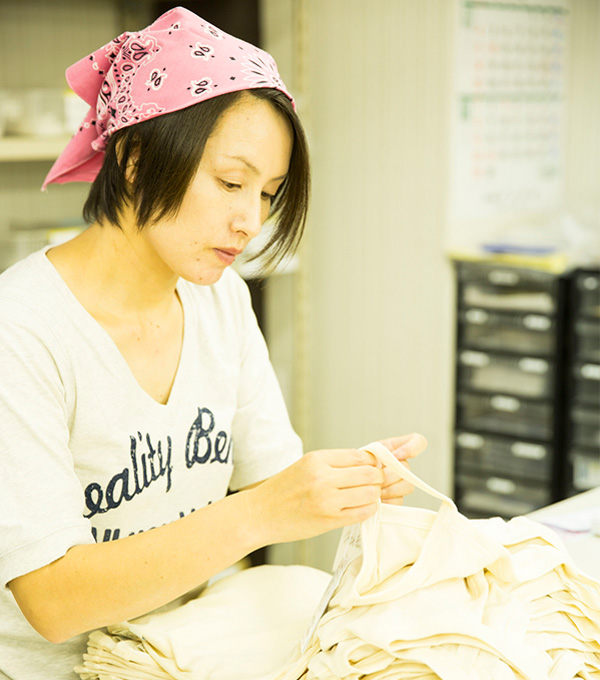
出荷前の最後の検品も、ひとりひとりが目で見て、手で触れ、チェックします。
ときには、厳し過ぎるくらいに感じる検品を続け、品質を保持することで、お客様からの信頼が得られるのだと考えます。
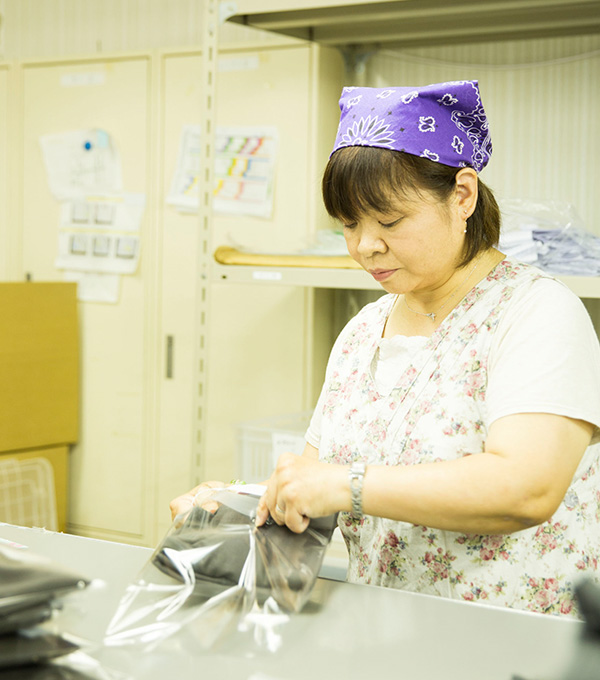
検品が終ったら、「喜んで使っていただけますように……」との願いを込めて、1点1点タグを付けて、パッケージに収めます。責任を持ってお客様の手に届くよう、すべての作業を工場内で行っています。
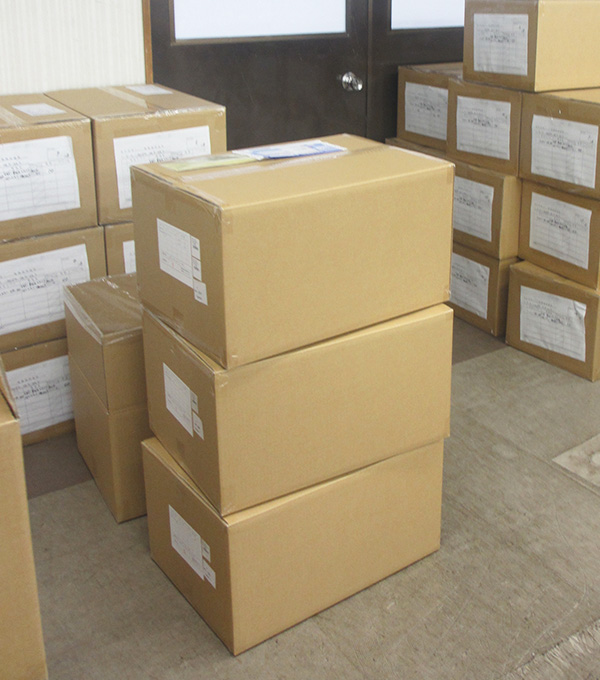
ここから配送業者の手に渡り、全国のお取引先に送られます。
プロダクトストーリー
Fleepは、陸前高田市にある自社工場のシェリールで主に縫製されています。
とてもデリケートな素材、スマイルコットン®で作られているFleepは縫製にも高い技術を要します。
各担当者の声と共に、そのプロセスをご覧ください。
Fleepのデザインとパターンメーキングは、秩父市の本社で行われ、そこで完成したパターンが、縫製工場のPCに送られます。そのパターンのデータを生産数に応じてマーキング(パターンを生地巾に合わせてレイアウトすること)して、プロッターから出力します。

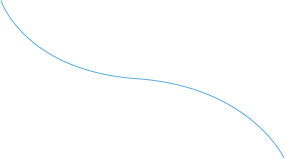
巻いたりたたんだりして納品された生地を、裁断しやすいように、生地巾に応じて2台の自動延反機を使って広げ、重ねていきます。「寸法通りの商品に裁断・縫製するために、生地の縮みや余計なクセを取り除くのが延反です。ハリのある素材なら、延反機が布を広げるのを待つだけでいいのですが、スマイルコットン®は軽くて柔らかいため、布が重なったりシワになりやすいんです。それを目で見てチェックし、手で伸ばしていきます。手が荒れていると繊維に引っかかり傷をつけてしまうため、日頃から注意しています。気になる場合は薄手の手袋をして作業することもあります」
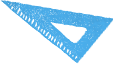
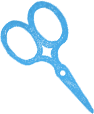
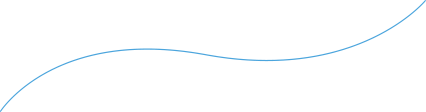
出力したパターンを、延反した生地の上に配置します。
「通常の生地だと25枚程度重ねますが、スマイルコットン®は多くても20枚程度。柔らかく滑りやすいため、どうしても重ねる枚数は少なくなります。そのぶん効率は悪くなるのですが、裁断でミスがあると後の作業すべてに影響するため、慎重に行います」
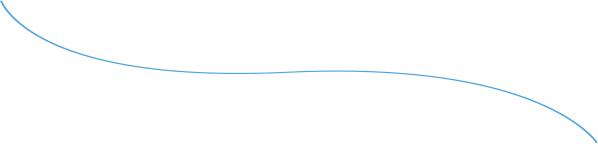
自動裁断機(CAM)を使用して細かいパーツ毎に、生地を裁断します。
レースは巾、柄の大きさや方向性によってパターン配置が変わるため、細かい手作業での裁断が必要になります。

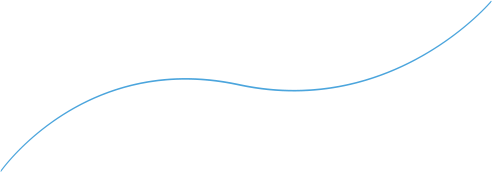
主力となる陸前高田市の縫製工場では、7種類のミシンが約100台並んでおり、約60名が一針一針、着用していただく方々のことを想いながら、心を込めて縫製しています。Fleepの商品はシンプルに見えても、肌あたりを考慮した複雑な縫い方になっていて、多いものでは40工程以上になります。
「Fleepが誕生した2007年から担当しています。それまでも下着を縫っていたので、伸縮性のある素材や薄い素材には慣れていましたが、スマイルコットン®の柔らかさに、最初はとても苦労しました。
縫うときの布を引っぱる加減などが、他の素材とはまったく違うんです。たぶん通常の2倍くらい時間がかかっていたと思います。始めは納期に間に合うか、本当に心配でした」
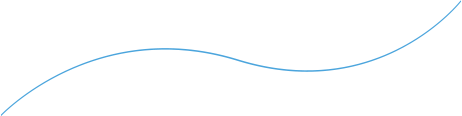
「1989年からこの工場で下着を縫っていますが、スマイルコットンを初めて縫ったときは、その伸縮性の感覚をなかなか掴めませんでした。
今まで扱った中でいちばん苦労した素材、と言えると思います。縫いしろ部分をフラットにするためには、この柔らかくて滑りやすい素材を6枚重ねて縫うこともあります。
始めは苦労しましたが、満足できる仕上がりになってからは、他の素材を縫うより楽しくなって。不思議なものですね(笑)」
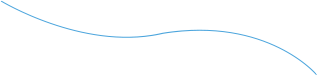
「Fleepの縫製は、他の製品に比べて工程が多いのが特徴です。工程が多いということは、ひとつの工程でわずかでもズレが起きると、それが少しずつ重なって最終的には大きなミスになるということです。
“最初のひと針がいちばん大切”。チーム全員が、その気持ちで縫っています」
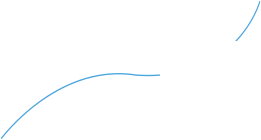
「Fleepは縫い目を表に出して縫製します。つまり、普通の製品とは表裏がすべて逆なんです。 縫製に慣れている者ほど、始めはこれに戸惑い、慣れるのに時間がかかりました。
途中で『表裏を間違えている!』と、ハッとしたことが何度も。今では、Fleepの縫製に関わる全員が、それを体で覚えています」
「重ねた生地の枚数、縫う箇所によって、ミシンの目調子を微妙に変えています。濃色は目調子を少し緩くしたり、同じ生地でも色によって加減が変わるんです。それは、生地と会話しながらの作業という感じですね。少しでも縫いやすいように、機械担当と相談しながらミシンのアタッチメントを改良することも。皆で工夫しながら、縫製の現場でも改善を重ねています」
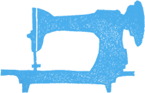
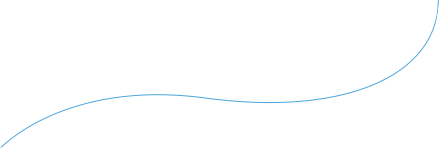
「通常、衣類の生産というのは、作業の内容と流れを固定して、一人が同じ場所で同じ工程を繰り返し行うほうが、効率が良く生産性も上がります。でも、Fleepは縫製の内容が細かいため、固定したラインをあえて設けず、フレキシブルに組み替えています。それが互いの仕事を理解することにもなって、チームワークも強くなるようです」
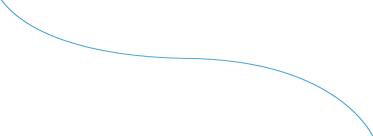
出荷前の最後の検品も、ひとりひとりが目で見て、手で触れ、チェックします。
ときには、厳し過ぎるくらいに感じる検品を続け、品質を保持することで、お客様からの信頼が得られるのだと考えます。
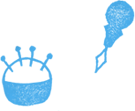
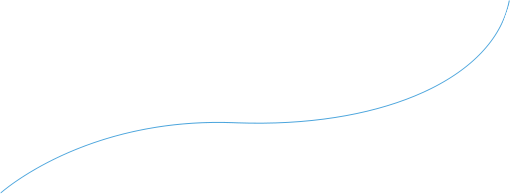
検品が終ったら、「喜んで使っていただけますように……」との願いを込めて、1点1点タグを付けて、パッケージに収めます。責任を持ってお客様の手に届くよう、すべての作業を工場内で行っています。
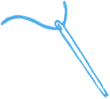
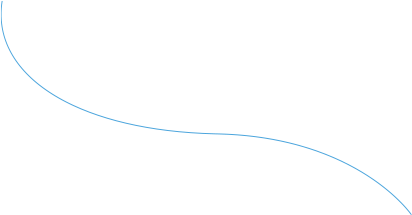
ここから配送業者の手に渡り、全国のお取引先に送られます。